Meeting the Quality Requirements of
Our Customers
At the heart of our Quality Assurance program is our internally developed data management software. The casting process can be complex and the key to producing consistently high quality castings is determining the best practice for each step in the process and then consistently repeating that best practice. We log each step of the production process on each new item produced. All new items enter the system as “yellow light” (caution) items. Special care is taken to ensure the documentation of each step in the process and once best practice is determined, and we have captured that information, the product is green lighted. Future orders will be produced utilizing the same processes (e.g. pouring temperature, time to shake-out, core sand type etc…).
Often times a fixture, or go/no-go gauge, is required to ensure proper fit of the casting; that information is logged and the fixture/gauge is marked and catalogued. We also log critical attributes for each item and QC to the critical attributes.
At Wear-Tek we place the highest priority on information management and providing the necessary production information to everyone on the shop floor. As a result you can count on a consistently high standard of quality, with minimal variation from one order to the next, regardless of the time interval between production runs.
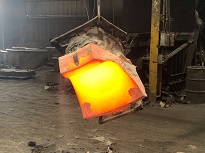  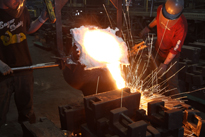
|